At the end of April 2024 there was yet another announcement in the autonomous robotics space. This one was called the Astribot S1 by a company called Astribot, and you can see the full promotional video above (worth checking out!). We are no doubt in a period of exceptional progress in computer intelligence with companies like Boston Robotics and Waymo pushing the envelope of autonomous robotics. Needless to say, the Astribot announcement didn’t go unnoticed by social media pundits. Almost immediately our feeds were filled with posts claiming that the Astribot S1 was nothing short of a revolution, a technical breakthrough which will completely revolutionise our kitchens.
I’m here to bring you some bad news. The robot shown in the video is very unlikely to become a genuine shippable product anytime soon. As a 20+ year veteran in the computer vision industry I’ll also do my best to explain why I believe it is a prototype with little autonomous or genuine real-world interaction capability, and unfit for safe operation around humans.
Deconstructing the Astribot S1 “Hello World” video
For a robot (such as what the Astribot S1 aspires to eventually become) to be able to interact with the real world, it requires a good understanding of the world around it. For this you need computer vision and a sensor stack which typically includes i) depth sensing for estimating world scale, ii) some standard cameras for intelligent identification of objects and surroundings (so-called object segmentation or instance segmentation), and iii) ideally some infrared sensors for boosting low light performance, and so on.
Why is that significant? Because just by identifying what kinds of sensors the Astribot S1 has (and what their field of view is), we can predict the theoretical extent of its capabilities!
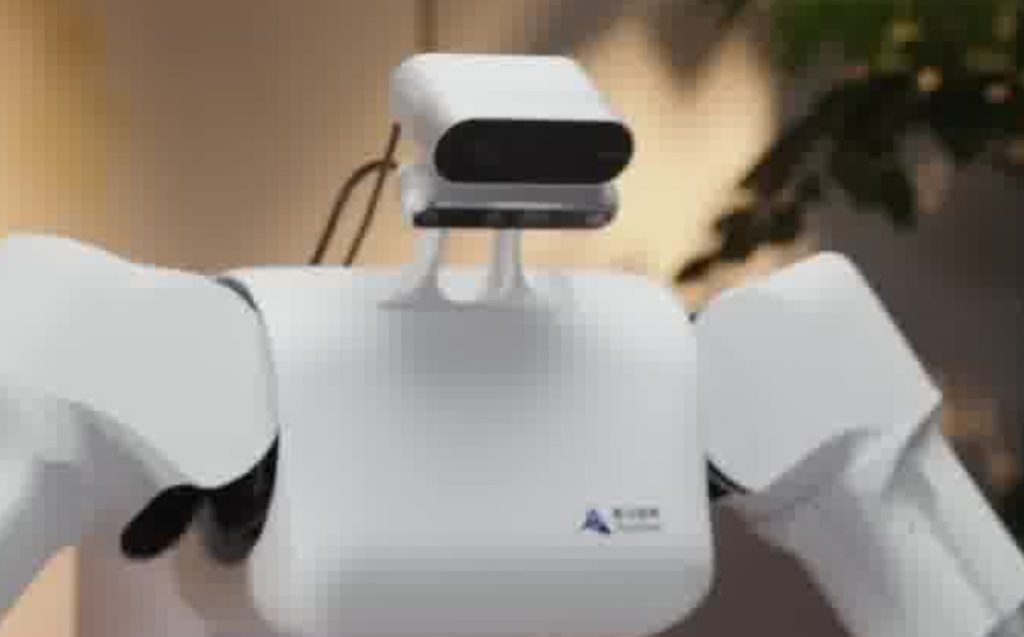
The robot only appears to have two sensor modules attached to it, both above the robot’s body.
- The top sensor looks very much like an Orbbec Femto Bolt – this off-the-shelf sensor package combines a high resolution RGB (colour) sensor and a Time of Flight (ToF) depth sensor.
- The sensor just below it looks like an Intel RealSense device of the D-family, possibly an Intel RealSense D415? (would need to see it up-close to say exactly which one it is – could for example also be a D455) – this would likely also carry one RGB (colour) sensor, and two infrared cameras for depth estimation.
Both sensors are pointed downwards, which will limit their ability to see very far, and especially the Intel RealSense-looking device can only be expected to see the immediate “table” area (its maximum vertical field of view or FOV would be unlikely to exceed 45 degrees). This should immediately be a red flag for anyone expecting this robot to be capable of operating safely in a human environment in its present form – the robotic arms are powerful, and the potential field of view of the robot’s vision system is quite limited!
One additional point about these sensors is that it’s unusual for an actual product to integrate them in this kind of off-the-shelf form factor. Typically they would be integrated as modules (basically the PCB+sensors without the outer shell) into the product’s final design. This fact alone makes the robot look like a prototype!
So, now that we have a hypothesis of the limited sensor capabilities of the robot as our starting point, let’s look at the video in a bit more detail!
The smoking gun – the scene where the robot is interacting with an area it cannot possibly see!
Being familiar with contemporary CV products I immediately noticed that the sensor which resembles the Orbbec Femto Bolt isn’t actually switched on at any point in the video! Why is this an issue? Take a look at this scene where the robot throws a paper plane into a bin:
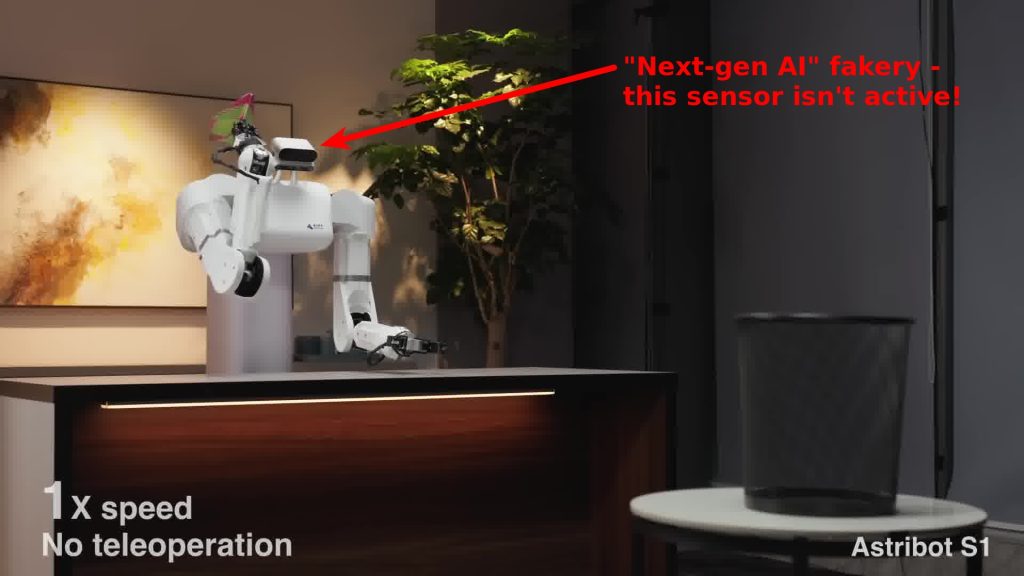
Given that the Femto Bolt-looking sensor is the only one which could even theoretically “see” the bin in the scene captured above, if the sensor is in fact off then it is evident that the robot is performing the task blindly and in a pre-programmed fashion. And if that’s demonstrably true for this scene, why would it not be true for all the other scenes in the video?
How do I know the Bolt isn’t capturing any live data in the shot?
Whenever a Femto Bolt sensor is actively capturing data, a small LED lights up in the front panel of the device, like so:
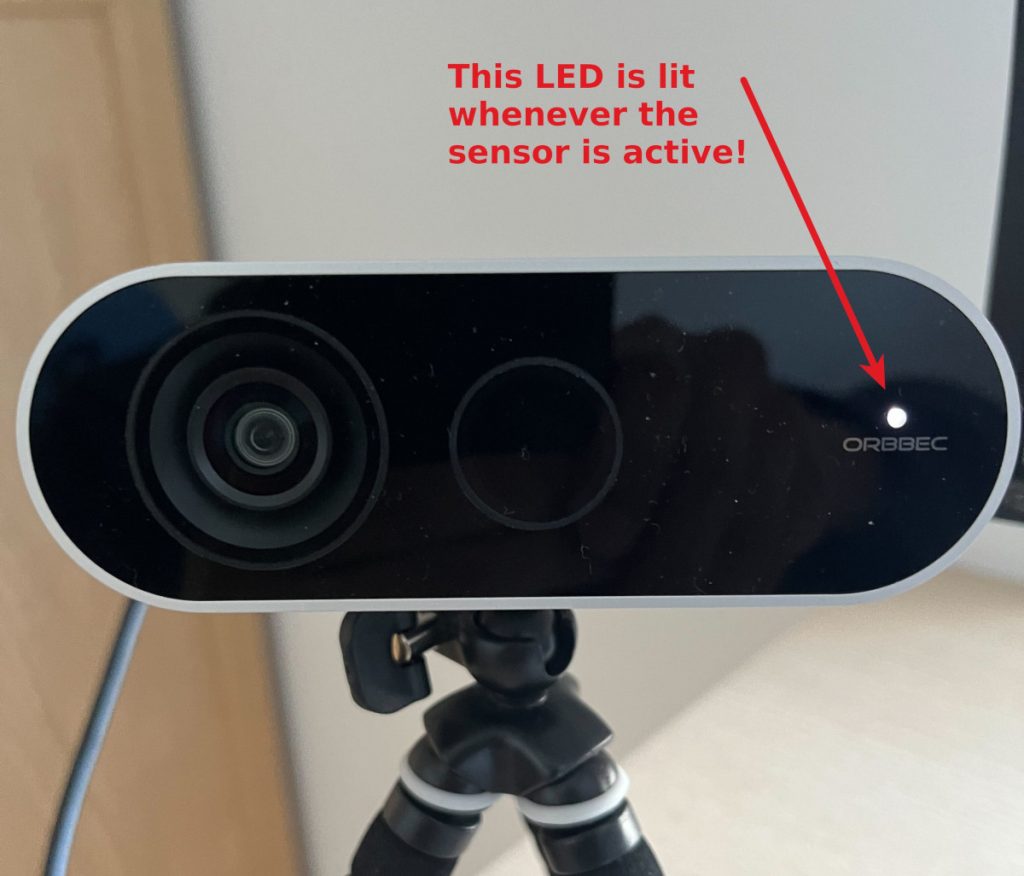
Note that no such activity LED appears in a single frame of the Astribot S1 “Hello World” video! Basically, everything this “Next-gen AI Robot” supposedly is capable of doing, it is miraculously performing without even the top sensor being on!
More oddities
Other aspects in the video stand out as suspicious for a system which is supposedly capable of performing robustly in the real-world. Below are more examples:
Example 1: Non-robustly mounted sensors.
Take a close look at what happens to the sensors when the robot is moving quickly:
If you look closely at the cameras on top of the robot in the cup-sorting sequence, you will notice them shaking like crazy whenever the robot arms are accelerating or decelerating quickly. This might be okay and perhaps acceptable for a first prototype, but this would be one of the first mechanical issues I would tackle if I were building machine vision for a robot like this! The sensor shaking causes a loss of accuracy due to motion blur, rolling shutter artifacts, and so on. Maybe fine for a crude first prototype of a robot, but not acceptable for a robot that’s designed for safe interactions with humans in the real world!
Example 2: The difficult stuff is never shown in the video!
Another suspicious aspect is that the genuinely difficult computer vision tasks always happen off-camera. Take this scene with the glass decanter for example:
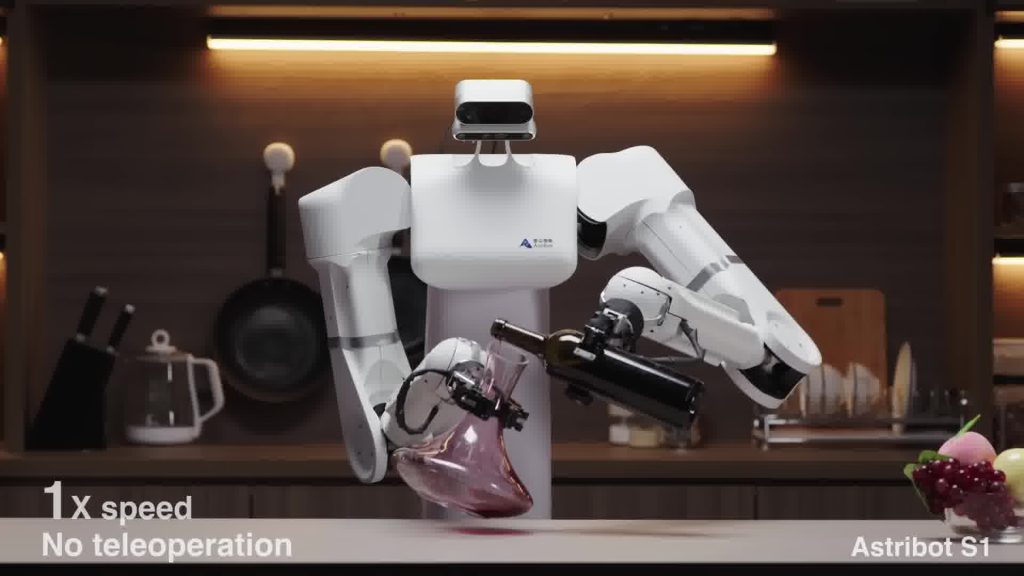
The scene starts with the robot already firmly holding the glass decanter, and there is no indication of how it got there without the robot accidentally crushing it! In this promotional video all the hard stuff happens off-camera, but the decanter shot is particularly suspicious because transparent objects would not typically register very well in the sensors that the robot is equipped with.
Although I can’t tell from the video exactly what sensor model is observing the table (I did speculate it potentially being a D415 or D455), the Intel RealSense family of sensors would regardless carry out depth estimation and mapping using one of two approaches: i) Time of Flight (often called ToF, sometimes LiDAR) which is used in the RealSense L-series, or ii) Stereoscopic depth, which is the method used in the RealSense D-series. Let’s quickly check what a glass object would look like in either type:
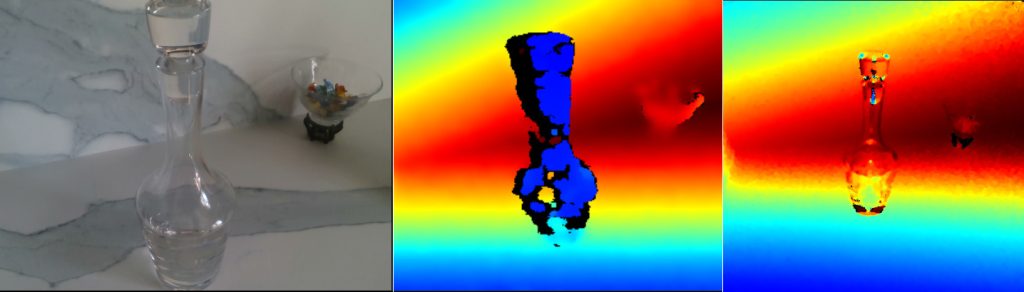
The depth map of a stereoscopic D-series RealSense can be seen in the center of the above 3 images. The colour gradients represent a range of distances. The black areas in the depth map image are undefined and contain no data at all, so for a sensor of this type the blotchy blue data would be all that’s visible of the carafe! On the right side we can see the depth map from the ToF-sensor of an L-series RealSense. With this sensing approach the carafe barely registers any depth at all – it looks like a ghostly magnification of the contours!
Astribot promises a +/- 0.03 mm precision for the robot, and this could well be true for the robotic arms (these are after all an off-the-shelf technology). But, in order for this kind of precision to be effectively applicable in an autonomous setting the CV sensing stack needs an order of magnitude more precision to be able to effectively interact with the world!
A true test for the robot’s vision would be to present it with a variety of carafes, bottles and decanters of different thicknesses in random locations and observe if the robot can successfully and autonomously grab them all without dropping or crushing them. But, given there is no indication of sufficient vision capability existing in the robot I strongly doubt we’ll see a real-world live demo of that kind anytime soon!
Example 3: The “no teleoperation” teleoperation demo.
There is a wild segment in the video where a person is shown (superimposed) waving their arms, with the bot seemingly following and repeating the movements. We can be certain that this isn’t a real time demo, not least because of the “smoking gun” realisation that the only sensor mounted on the robot which theoretically could even see the person (i.e. the Femto Bolt) is switched off!
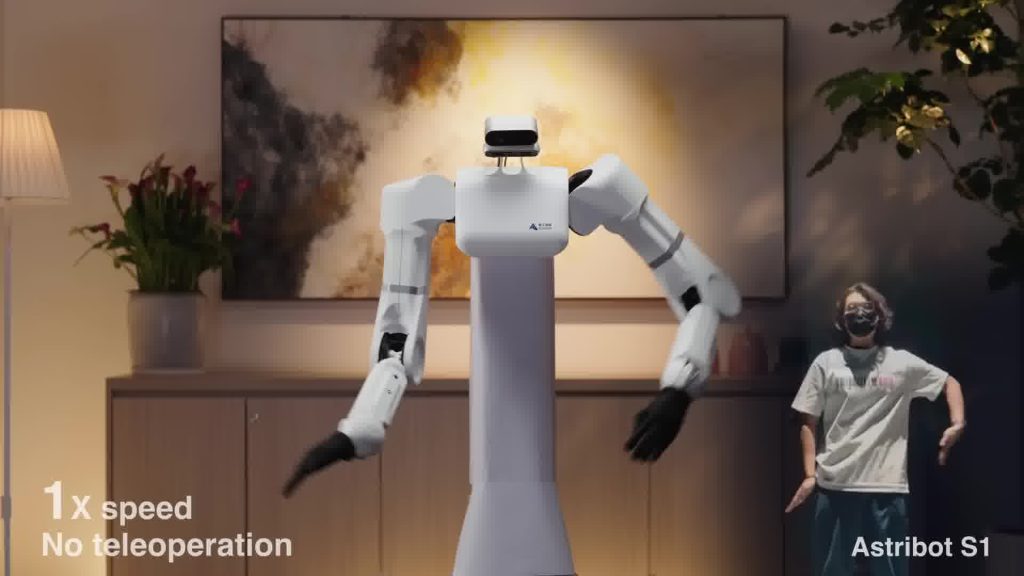
Purely as a marketing message I am confused what this particular scene is supposed to demonstrate in the “1x speed no teleoperation” bot. That it is possible/necessary to teleoperate the robot after all?
In the clip there are a few interesting details which can help us deconstruct what we are actually seeing! In the above still frame, note how the hand orientation (roll) is not captured particularly accurately (compare the robot vs person hand roll!). If I had to speculate what was done (based on the little information we have) I would guess:
- The company appears to own an Orbbec Femto Bolt. It stands to reason the company would leverage off-the-shelf libraries available for the sensor (as that is typically the quickest way to get prototypes done quickly!)
- As it happens, Orbbec provides a software library called the Orbbec Body Tracking SDK . One of the limitations of this technology is that whilst the body tracking can reasonably estimate arm pose, it is less accurate in estimating hand rotation/roll!
- One cold engineering fact of building systems like this is latency. The Orbbec Femto Bolt sensor has a fair bit (80+ ms depending on imaging resolution!), and even the robot control interface would likely have some overhead. Although there are ways to mitigate latency in real-time systems, it is still interesting to note that there’s near-zero latency between the robot and the teleoperator in the video!
- Putting two and two together, my best guess for how this clip was created is that i) the operator sequence was pre-recorded with a Femto Bolt, ii) the body movements were converted into motion capture data using the Orbbec Body Tracking SDK, iii) this data was imported into the robot’s control software as a pre-recorded sequence – but with limited/missing hand roll data, and iv) the two separate takes were then combined in post-production to make it look like it was a real time “1x speed” event taking place. Again, misleading marketing at best!
Just to give you a sense of how much work it is to pull off something like I just described, a computer vision engineer with familiarity of how to program the robot (this can often take a few days of study!) could probably cobble together something like the above in a couple days of work. The end-result may look cute, but it’s definitively not “Next-Gen AI Robot”!
Example 4: UI which is too fancy for what it is purporting to be.
There is a sequence in the presentation which appears to be representing intelligent AI-like reasoning by the robot. The angle of the camera lines up with what I would expect to see through the Intel RealSense’s RGB (colour) sensor:
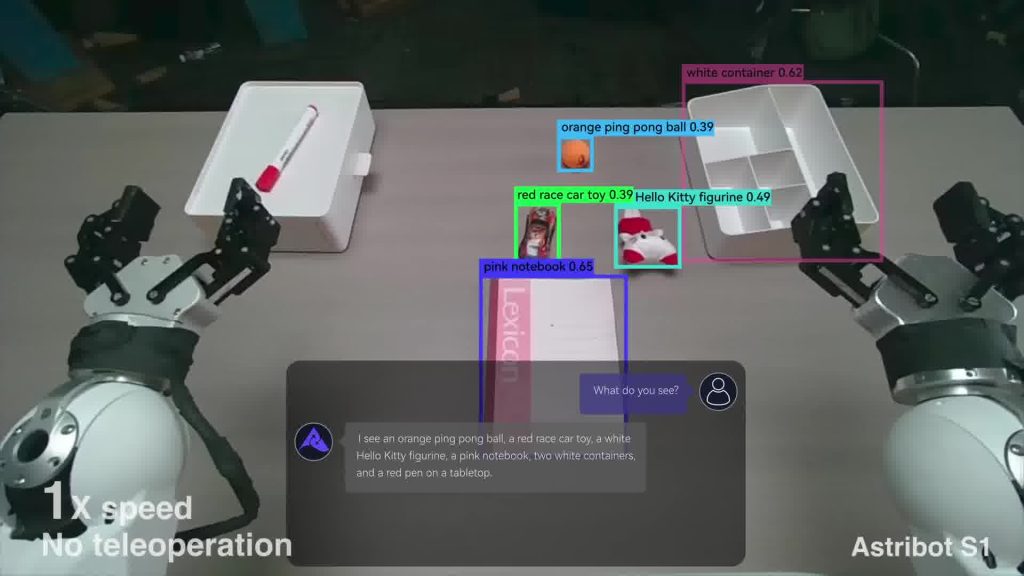
So-called object segmentation (which aims to identify classes of objects with some % of confidence) is a standard computer vision (machine learning) technique, and many powerful off-the-shelf libraries exist (such as the awesome YOLO for basic object detection!). However, what caught my eye is that the sequence of events in the video doesn’t reflect real-world model behaviour. A few issues stand out:
- The classification is suspiciously specific, listing object classes such as “red race car toy” and “Hello Kitty figurine” – this is not how generic object classification is done! Training complexity increases for every class you add into your training set, and so in the real world the categories tend to be quite generic (think “airplane”, “car”, “van”, etc). For sub-class identifications other methods could be chained to the processing pipeline, but I see no indication of that having been done here!
- The segmentation results visually fade in step-by-step. This, again, is not how object segmentation works in the real world! When running neural network inference you get all the results at the same time.
- Building on the point of how oddly the segmentation results fade into the sequence (remember that this is supposed to be an “1x speed” capability demo!), the window at the bottom which is portraying an LLM chat dialog already seems to have the complete segmentation information in advance, before the results have even been registered on screen! Strange huh?
- Finally, if the inference really is as slow as it’s presented in this sequence, just imagine how terrifyingly dangerous the robot would be to any humans working around it! The robotic arms are fast (Astribot claims 10 m/s!) and strong enough to break human bones, which means that the robot would need to be able to reliably detect a human arm in its vicinity in 20 ms or even much less! Assuming that the Intel RealSense sensor in itself has latencies around 20 ms (several ms for frame exposure, a few for VPU depth etc processing, some for USB transmission, plus the OS overhead) , that doesn’t leave many milliseconds for running frame inference and halting a robot arm that is about to crush your sous chef’s hand!
In summary, this entire sequence looks like a post-processed overlay animation (i.e. CGI fakery!) rather than a genuine version of what it is trying to present (such as a “1x speed” object segmentation model combined with an LLM exploiting the emergent capabilities of such a hybrid). It is also plainly obvious that this robot – with its current sensor capabilities and latencies – couldn’t operate safely around humans!
Example 5: Inexplicable loss of 3D instance segmentation capabilities
Continuing the theme of the video never showing anything genuinely difficult (computer vision-wise) happening on-camera, there is a part of the video where the robot is presented as being capable of generating a 3D instance segmentation map of diverse objects on the table, and then manipulating/organising these. One thing which strikes me as odd is that the instance segmentation results vanish from screen as soon as the robot starts to perform the sequence. Check the start frame:
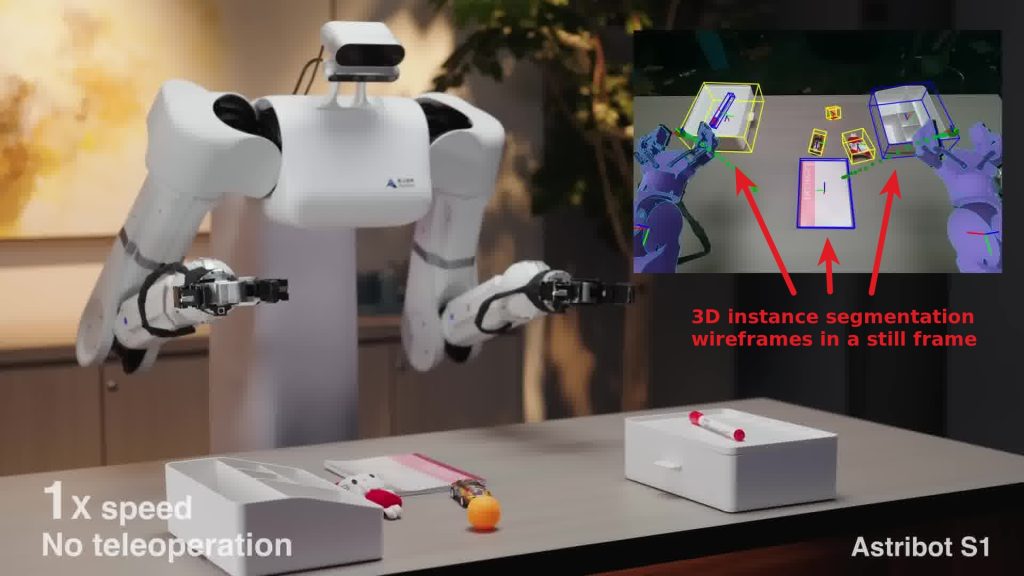
At first things look like expected, you can see 3D instance segmentation bounding boxes in the top right image above. But now see what happens when the robot starts to execute the sequence:
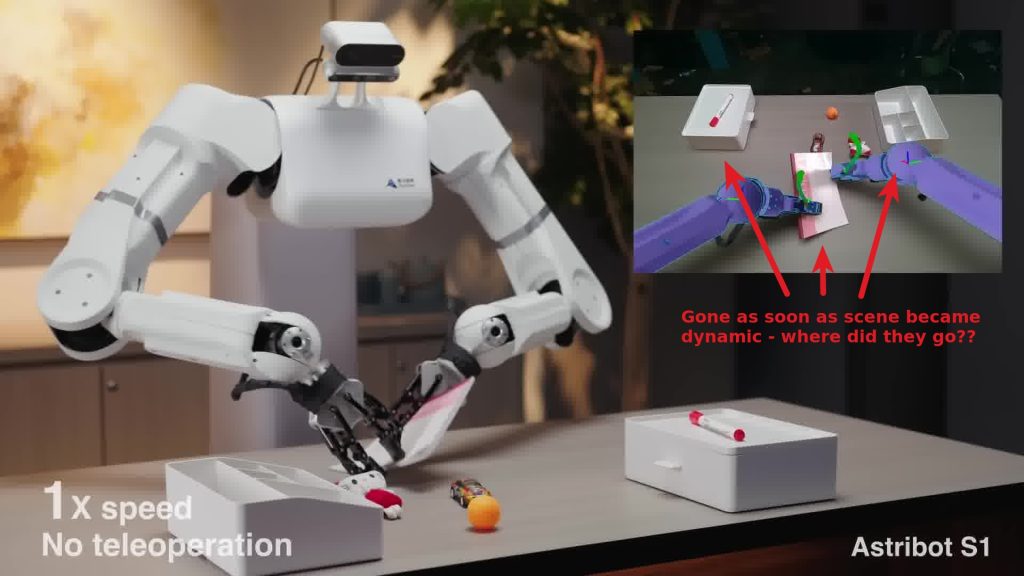
When the robot starts moving the 3D instance segmentation overlay vanishes! Is that because the sensor latency would make them misaligned? Is that because the robot struggles to accurately identify and delineate the objects mid-sequence? (And how would the robot interact safely and autonomously if so?) Or could it perhaps be that the company actually doesn’t have any robust 3D instance segmentation capabilities at all and that the initial wireframe presentation was simply overlaid in post-production (i.e. more visual FX fakery)?
Whatever the explanation is, given that other sequences in the S1 promotional video are (due to vision limitations) obviously pre-programmed, given that at least one part of the sensor stack (i.e. the Femto Bolt) is inactive the entire time, and given that the “Next-Gen AI Robot” capabilities presented even in this clip really do not show anything remarkable in terms of computer vision capability, I’m leaning towards assuming that even this seemingly impressive sequence is simply some painstakingly pre-programmed “AI theater” which is replayed enough times until the camera gets its “money shot” for the promotional video.
Conclusion
For the kind of system portrayed in the Astribot S1 promotional video highly advanced and robust computer vision capabilities would be required in order for it to autonomously perform a diverse range of interactive tasks in the real world.
Nothing presented in the promotional video indicates that the company possesses such capabilities, and if anything the video carries plenty of clues to indicate that the S1’s vision capability is nonexistent.
Additionally, for such interactions to be safe around humans, the sensor latency and coverage would need to be substantially improved. A robot arm moving at 10m/s is moving 10 mm (0.4 inches) per millisecond! A sensor like the Intel RealSense would typically run at 30-60 Hz for the kinds of resolutions shown in the video, which basically means that one video frame is captured every 33 milliseconds. How close to the (supposedly) autonomous robot would you be comfortable standing?
So, what to believe? Luckily we can apply Occam’s razor for determining the most likely explanation for what we’re seeing in the Astribot S1 video! There are at least two alternatives:
- A new startup company has secretly solved all of the most difficult problems in AI, latency, robotics and computer vision (problems that not even Tesla’s Optimus team has been able to solve yet), and is now ready to start shipping their stationary kitchen bot.
- A new startup with little or no actual genuine capability created a “fake it until you make it”-type PR video stunt in the hopes of generating hype and getting investor money to try to eventually build a real robotics product.
I am curious to hear which option sounds more plausible to you?